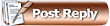 |

07-21-2009, 01:24 PM
|
|
|
Join Date: May 2009
Location: Onoway @ Bigriver(SASK)
Posts: 650
|
|
Owwwww
Had a fight with a concrete loading ramp in 4ft waves and lost big time  Who is the best to weld on a new skeg on my Yamaha 250,? , nead a new bowlifting 21 pitch SS prop too.  Edmonton Area
__________________
MR WALLEYE BOB
|

07-21-2009, 01:41 PM
|
|
|
Join Date: May 2009
Location: Calgary
Posts: 326
|
|
Send a PM to sandalius he is a welder AND a helluva nice guy!
|

07-21-2009, 01:46 PM
|
 |
|
|
Join Date: Nov 2007
Posts: 259
|
|
I know some one very close who will fix it but it will cost you.
|

07-21-2009, 02:01 PM
|
|
|
Join Date: Mar 2009
Location: Edmonton
Posts: 9,686
|
|
Repairs
Budget Prop Rebuilders is someone you can call. Their address is 5921- 91st in edmonton. Ph # 780-434-6777. If they cant help you they should be able to direct you to who can.
|

07-21-2009, 02:20 PM
|
|
|
Join Date: Mar 2008
Location: Fort Saskatchewan Ab
Posts: 8,926
|
|
Id suggest geting someone that can Weld alluminum , Contact the boys at Kenfirm manufacturing in Ardrossan maybe they can help you out , or Call up the welding program at nait as they have experts that weld Aluminum youd hate for someone who thinks they know and burns a hole threw your boat .
|

07-21-2009, 05:29 PM
|
Banned
|
|
Join Date: Aug 2008
Location: slave lake
Posts: 4,221
|
|
he was talkin about the motor bbj and not the boat itself. I dont know if nait farms out thir instructors but they would probably be able to tell you who is best qualifyed. Without seeing the skeg I could not tell you how hard its going to be. How thick is the metal and what is it made out of? If a magnet does not stick to it it is aluminum or stainless, If it sparks when you grind it its stainless and not aluminum. That will give you a rough idea of what your dealing with.
|

07-21-2009, 05:32 PM
|
 |
|
|
Join Date: Aug 2008
Location: edmonton
Posts: 604
|
|
i believe that some skegs/ outboard housings are magnesium
cheers
__________________
Fishermen know that the sea is dangerous and the storm terrible, but they have never found these dangers sufficient reason for remaining ashore." Vincent van Gogh
|

07-21-2009, 05:43 PM
|
 |
|
|
Join Date: Apr 2008
Location: Alberta
Posts: 1,731
|
|
you most likely can tell by my handel im a welder as well im a shop foreman, unfortunately im in Red Deer. if you want shoot me a pm and send me some pics Im sure I could help you out for free if your willing to head down this way pick up some beer and take me and anouther guy out for a day fishing.
|

07-21-2009, 07:13 PM
|
Banned
|
|
Join Date: Aug 2008
Location: slave lake
Posts: 4,221
|
|
Lol if its magnizium dont touch it! Trying to weld that is a rather SPECTACULAR excercise in futility and will leave you sick as hell.
|

07-21-2009, 09:07 PM
|
|
|
Join Date: Jun 2009
Posts: 166
|
|
check with bass pro or cabelas. they sell a bolt on skeg repair kit. just put skeg in the search area of their website and it will come up. that will look way better than welding it. the prop might be repairable. there is a guy in airdrie that does good work.
|

07-21-2009, 11:29 PM
|
|
|
Join Date: Jun 2009
Posts: 7
|
|
i have fixed many skegs on all sizes of engines they are usually all weldable as long as you didnt break it off too high. we keep wet rags on the case to prevent any heat damage to the internals. Charchun Welding 9178 yellowhead trail. 471-4290. Bring your boat by i will give you a estimate . i can fix some props, if they are only slightly damaged, if they are really bad i take them to budget prop repair as he has the dies and patternsto keep the pitch even on all blades. Casey
|

07-22-2009, 02:01 AM
|
 |
|
|
Join Date: Mar 2008
Location: Edmonton, Alberta.
Posts: 196
|
|
Skeg
I use a guy in Edmonton and i've had nothing but great things to say about his work, also i've referred at least four people to him over the past couple years and they have all had great experiences, this type of job should be done by someone who specializes in marine engine stuff, i have the abuility to weld alum my self and would touch my own, you have to know where and how much you can heat, and if you have to remove the leg to pull out components before welding you should have it done by a trained professional, anyways the guys i use are call Budget Prop & ATV, they are on 91st and about 60ave, look them up.
__________________
"Daj Bosze" !!!
|

07-24-2009, 07:38 PM
|
|
|
Join Date: May 2009
Location: Onoway @ Bigriver(SASK)
Posts: 650
|
|
 Thanks Guys for all the usefull info (still sad about my boat though  )
__________________
MR WALLEYE BOB
|

07-24-2009, 10:17 PM
|
|
|
Join Date: Jul 2009
Location: Edmonton
Posts: 127
|
|
if a magnet does not stick it is because there is no ferrite(Fe) in the composition, no rust oxides, but it could be any number of base metals or more likely an alloy. and to weld aluminium you will need high frequency welding machine, not that common, due to the "soft" characteristics of the material
|

07-24-2009, 11:23 PM
|
Banned
|
|
Join Date: Aug 2008
Location: slave lake
Posts: 4,221
|
|
Like I said that was a rough way of judging. It sure could be any number of alloys... and all the most comon ones are some form of stainless, although some series of stainless are magnetic. If your mig welding aluminum you dont need to use high frequency or AC power like you do when tig welding. The HF has nothing to do with the soft charecteristics of aluminum but is used to keep the arc going when the AC cycle crosses 0. As well it is used to stabilise the AC cycle which gets a bit lopsided when welding aluminum. Come to think of it Im not even sure HF is strictly neccessary for aluminum tig welding. But I do know for sure that I've used a spool gun to weld aluminum with machines that were incapable of producing either HF or AC power.
Last edited by Cal; 07-25-2009 at 12:01 AM.
|

07-24-2009, 11:56 PM
|
Banned
|
|
Join Date: Aug 2008
Location: slave lake
Posts: 4,221
|
|
Just looked it up on the miller web page, you can tig weld aluminum without HF. Theres a little more to it than that so feel free to look it up for yourself if you feel so inclined.
Last edited by Cal; 07-25-2009 at 12:04 AM.
|

07-25-2009, 12:17 AM
|
|
|
Join Date: Jun 2008
Location: Calgary
Posts: 852
|
|
Quote:
Originally Posted by Cal
Just looked it up on the miller web page, you can weld aluminum without HF. Theres a little more to it than that so feel free to look it up for yourself if you feel so inclined.
|
I would remove the lower leg anyway. Separate it from the upper and check everything out just in case.
Take the leg to a shop with a piece of 3/16" 5086 marine grade aluminum (if you don't have the broken piece) and you're good to go. Unless you are using a really decent welder and VERY HIGH end Spool Gun, I wouldn't even try to use MIG. The precision of a TIG machine is what I would use if I wanted it done properly. With the Lower leg off you won't have to worry about frying any of your electronics if using High-Frequency, which many welders prefer...
Just my 0.2 cents...
Cheers,
/FC....
|

07-25-2009, 05:14 PM
|
Banned
|
|
Join Date: Aug 2008
Location: slave lake
Posts: 4,221
|
|
You dont need HF to fry your electronics, regular DC or AC will do a pretty good job of that too. Dissconect the battery and keep the ground close to the weld and you should be OK. Done work for lots of companies that dont dissconect the batteries on their equipment, by keeping the ground close so the current doesnt get confused and run through the wiring I'v never had a problem.
|
Posting Rules
|
You may not post new threads
You may not post replies
You may not post attachments
You may not edit your posts
HTML code is Off
|
|
|
All times are GMT -6. The time now is 02:35 PM.
|